Is our growing need for cold storage sabotaging sustainability?
How one startup’s data-driven approach is cutting costs and slashing emissions for the cold storage industry.
Global cold storage needs are climbing to safeguard food, medicine, and critical vaccine supplies, but the industry already contributes 2.5% of global GHG emissions. By leveraging existing sensor data and machine learning, cooling efficiency can be improved, and electricity demand can be reduced, minimizing emissions and significantly cutting costs for the industry.
Want to learn more about the importance of cold storage? Check out our public research Notion.
Have you ever thought about what it takes to ensure that the food on your plate makes it all the way from the farm to the table? That farm might be on the other side of the planet, so for fruits and vegetables to travel those thousands of kilometers, we rely on cold storage to keep them fresh. However, cold storage doesn’t always work as we intend, and the amount of food lost due to a lack of adequate refrigeration is estimated to be 526 million tonnes yearly, or enough to feed one billion people.
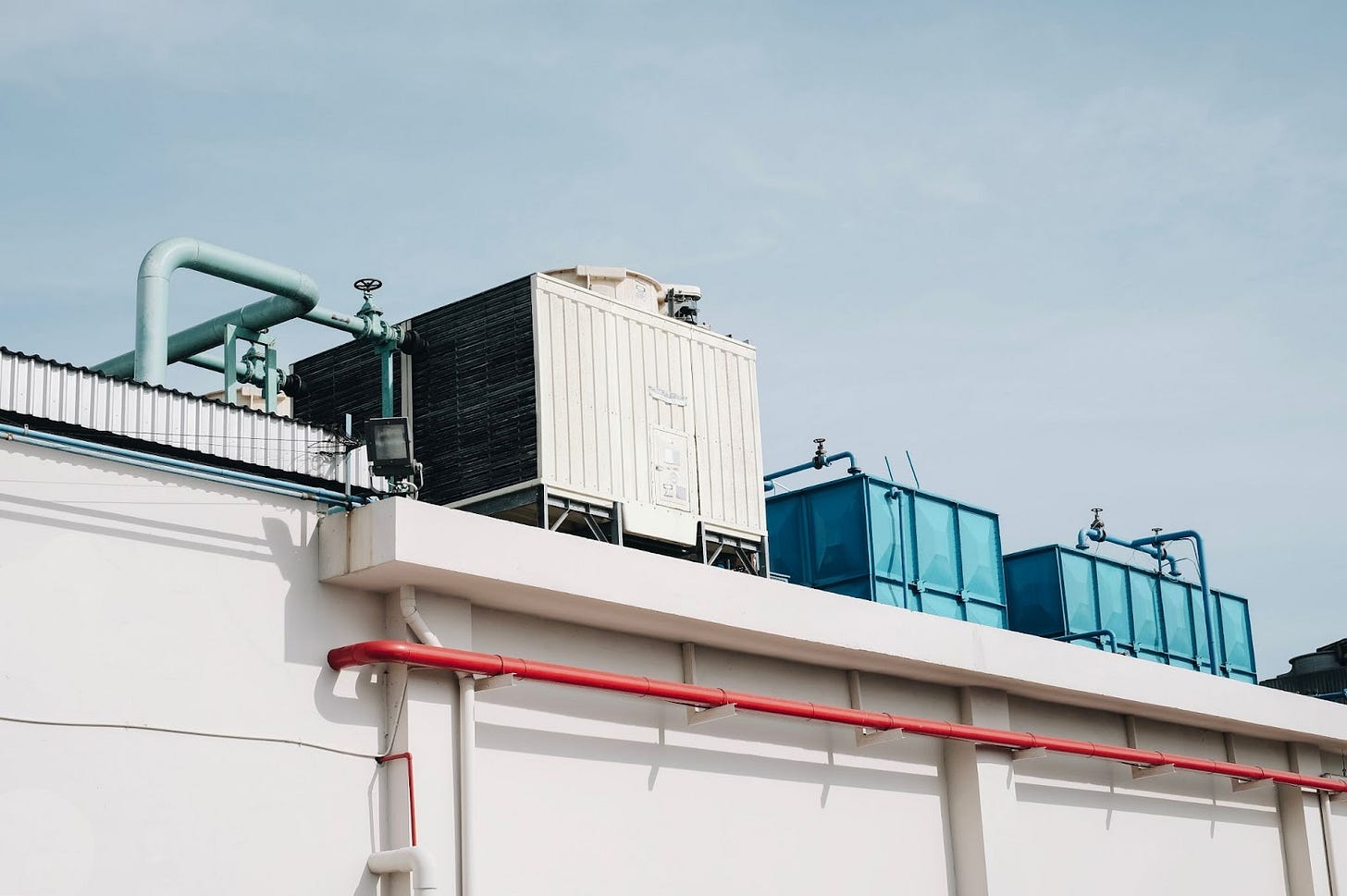
It’s not just food that needs to stay chilled. Modern vaccines have temperature requirements that range from -80°C to 8°C, and the slightest deviation from its specified window can become problematic quickly. According to the World Health Organization, up to 50% of vaccines are wasted every year, primarily because of failures within the cold chain system or a lack of access to adequate cold storage.
So, yes, refrigeration allows us to keep our food fresh and to store and transport vital medicines and vaccines, but unfortunately, these technologies are also some of the most emissions-intensive on the planet because cooling things down requires a lot of energy.
The cold storage paradox
The entire cold storage chain is responsible for an estimated 2.5% of global GHG emissions between energy consumption and refrigerants. In a cold storage warehouse, cooling processes alone can account for 60-70% of the electricity demands, with frozen warehouses using 30% more electricity than chilled (per capacity unit). A typical cold storage facility will use up to 9,960,000 kWh per year and emit up to 3,900 tonnes of CO2 in the process.
One of the biggest challenges is that a cold storage facility requires plumbing, electricity, ventilation, and insulation on a massive scale. What happens is that the components are literally pieced together like a puzzle by multiple suppliers and specialized workers, and each system is optimized for itself, not to work together with the other components. This places unnecessary strain on high-cost items like refrigeration compressors, significantly reducing their lifespan and increasing the electricity demands of the system as a whole.
Unfortunately, this isn’t an industry where the answer is to cut back because cold storage isn’t something we can do without. In fact, our needs are growing faster than ever. Cold storage is a $232 billion industry, and global capacity climbed almost 17% between 2018 and 2020, reaching 716 million m3. That’s 286,400 Olympic-sized swimming pools worth of cold storage and growing.
Transforming cold storage with data
In his 2014 TEDx Talk, Dr. Harvey Rubin, a leading voice in microbiology and public health, told the story of how his team came up with the idea to install vaccine refrigerators alongside cell phone towers in isolated parts of the world. Cell towers are everywhere, even in the most remote locations of developing countries, and the electricity there could be used to reliably power these vital cold storage devices and send alerts if something was to go wrong, and it worked!
Fast forward to 2020, the COVID-19 pandemic was putting a heavy strain on the vaccine industry. For one location in particular, Myanmar, civil unrest was making it difficult for teams to safely check on the vital refrigeration systems as often as necessary. So during one fateful dinner conversation with his son Benjamin, a government consultant for technology-driven solutions, it was suggested that those refrigeration units were likely collecting data from stock sensors that could be used to monitor the conditions from a distance. This was when the idea for SnoFox Sciences was born.
Bringing on Ben’s brother Matt, an expert in enterprise sales, is what really rounded out the SnoFox team and approach. Today, SnoFox is a data analytics company that uses the masses of sensor data collected from cold storage warehouses to create a custom digital twin of any refrigeration system. With this digital twin and its machine learning algorithms, SnoFox runs a detailed and comprehensive thermodynamic analysis of the refrigeration system, pinpointing where there are opportunities for increases in operational and energy efficiency. This means a cold storage facility can maintain its desired temperatures with lower electricity demand and less strain on its machinery.
The brilliance of the SnoFox approach is that all of this data is already being collected. There is no need for specialized sensors or new equipment. With SnoFox’s data-driven approach, cold storage facilities can improve facility cooling efficiency by up to 40%. So a SnoFox company isn’t only drastically reducing their emissions but also slashing operational and maintenance costs. And for an industry where a single company can spend upwards of $1 million on cooling costs alone, the benefits are massive.
We’re excited to be a part of the SnoFox journey and can’t wait to see this incredible team transform the cold storage industry for the better.
Want to dive deeper? Check out our public research on cold storage.